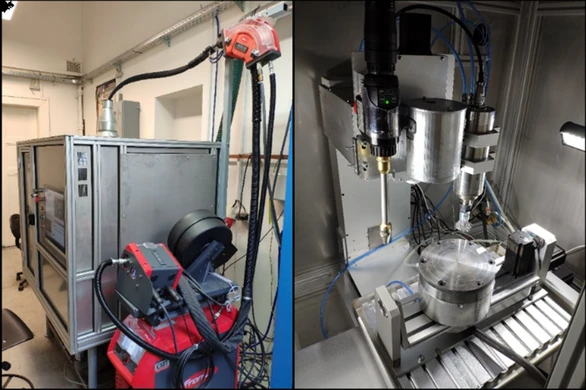
Wire arc additive manufacturing (WAAM) is one of the most productive metal additive manufacturing methods. One of its most promising applications holds in the manufacturing of difficult-to-cut materials where production costs can be reduced with minimizing the time of machining and total tool costs. To develop a correct WAAM, technological processes for manufacturing complex-shaped components welding torch path corrections and welding power corrections have to be made especially in critical sections such as corners and sharp edges. A predictive mathematical model of the material cladding during the WAAM process has been developed for the purposes of generating an optimal toolpath of the WAAM clads. This predictive mathematical model is simplified to reflect the important physical phenomena in the weld pool but also to optimize computing time. In this paper, the principle of the mathematical model is described, and its functionality is verified by the welding experiments with five different welding power settings. For the initial calibration of the model parameters single straight-line weld clads with 5 different welding power settings (wire feeds) ranging from 5.0 to 8.6 m/min were investigated. 3D scans of these welded samples are used for the verification. With the calibrated simulation model, it was possible to predict the precise shape with a maximum deviation circa 0.20 mm. The start portions of the weld clads seem more complex having the deviation circa 0.30 mm. These are valuable results as the WAAM technology is generally considered to be reasonably rough.