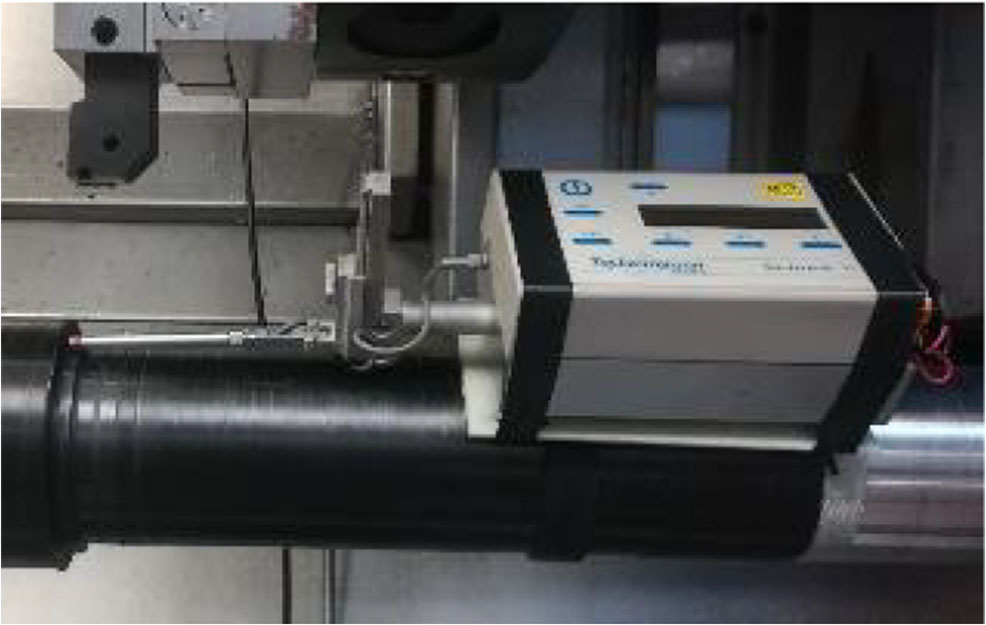
Turning of carbon fibre reinforced thermoplastic pipes is used for production of fluid ducts for the aerospace and oil industries. Although thermoplastics are chemically stable, the matrix could be affected by the heat introduced by the machining process. This paper presents how to measure cutting temperature using C/PEEK and C/PA12 material as examples. A suitable method based on a thermocouple circuit and electric conductivity of the carbon fibres is presented, including system calibration. Measurement uncertainties were established for this new method of calibration and measurement for both tested materials. The cutting temperature measurements were analysed by ANOVA and significant factors and its dependence on temperature were identified for further machining process optimization and determination of the predictive model equation. This mathematical cutting temperature model was estimated based on the measurements, and empirical coefficients were identified for selected statistically significant parameters for both composite materials. Because the measured temperatures were above the melting point, the machined surface, chips and structural changes of polymeric matrices were measured in order to prove heat affection.