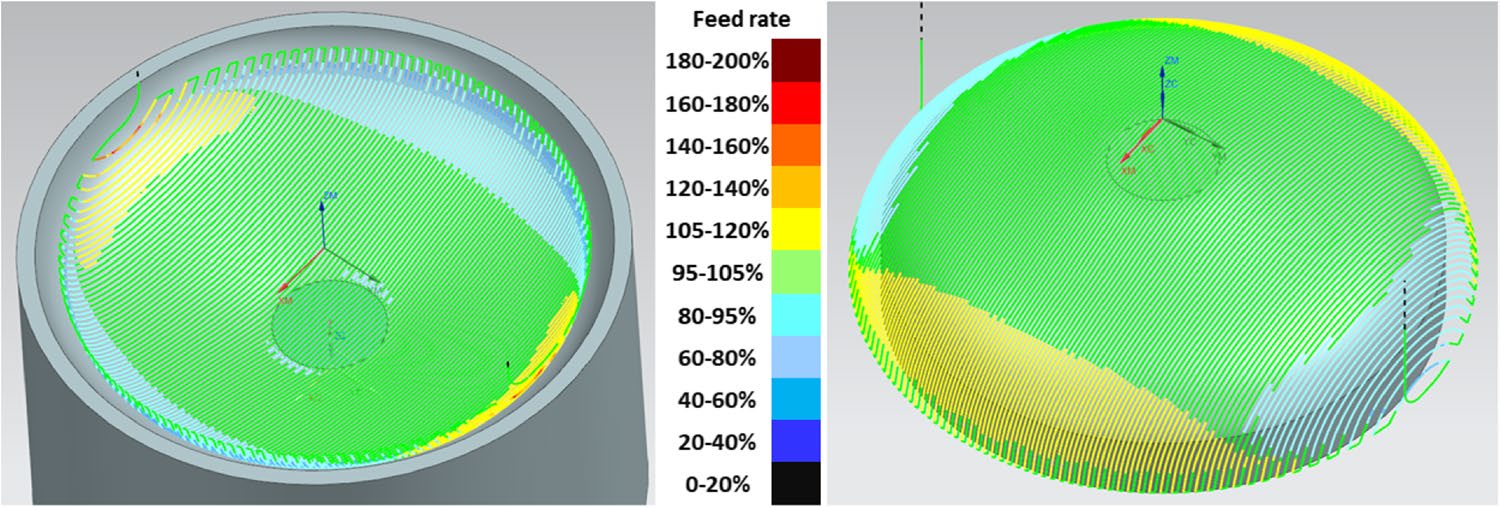
Constantly increasing demands for accuracy, surface quality, and higher production productivity associated with machining time reduction, all of which are to be achieved together with a cost-savings demand, create room for production optimization in complex part machining. This is especially true for difficult-to-machine materials, where great emphasis is placed on maintaining the technological conditions during machining, as the optimum value adjustment range is very narrow. When milling complex-shaped parts, the specified cutting conditions are not reached when the technological operation is set up for tools with a circular cutting edge. This is caused by the continuous change of contact point between the tool and the workpiece together with the fact that the cutting conditions are conventionally set to the tool reference point. Therefore, this paper contributes to the clarification of the feed rate control issue during point milling of complex-shaped parts and presents a feed rate optimization method to maintain a constant feed per tooth at the contact point along the entire toolpath. The proposed optimization method is based on the new derived relationship between the feed rate at the contact point and the feed rate at the tool reference point using the calculation of the actual pole of the movement of the tool reference point and actual pole of the movement of the contact point. This relationship is then used to recalculate the feed rate value at tool reference point to maintain the constant feed rate at contact point. The proposed method is then experimentally verified, and the advantages of applying this method are presented.