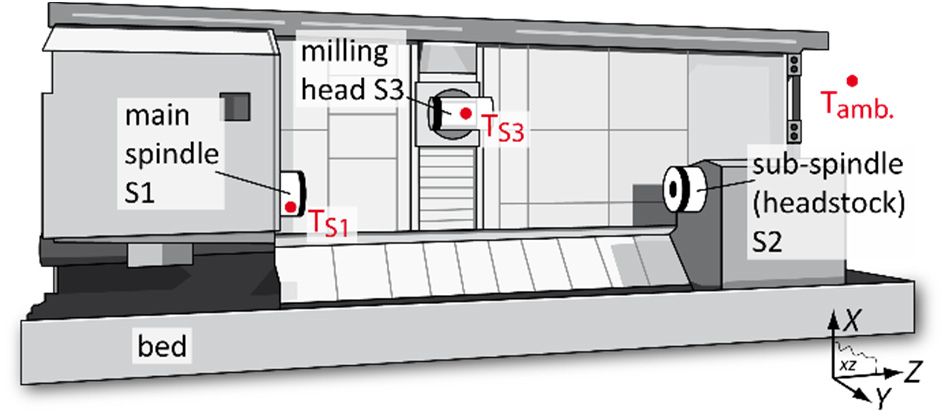
Achieving high workpiece accuracy is a long-term goal of machine tool designers. Many causes can explain workpiece inaccuracy, with thermal errors being the most dominant. Indirect compensation (using predictive models) is a promising thermal error reduction strategy that does not increase machine tool costs. A modeling approach using transfer functions (i.e., a dynamic method with a physical basis) has the potential to deal with this issue. The method does not require any intervention into the machine tool structure, uses a minimum of additional gauges, and its modeling and calculation speed are suitable for real-time applications that result in as much as 80% thermal error reduction. Compensation models for machine tool thermal errors using transfer functions have been successfully applied to various kinds of single-purpose machines (milling, turning, floor-type, etc.) and have been implemented directly into their control systems. The aim of this research is to describe modern trends in machine tool usage and focuses on the applicability of the modeling approach to describe the multifunctionality of a turning-milling center. A turningmilling center is capable of adequately handling turning, milling, and boring operations. Calibrating a reliable compensation model is a real challenge. Options for reducing modeling and calibration time, an approach to include machine tool multi-functionality in the model structure, model transferability between different machines of the same type, and model verification out of the calibration range are discussed in greater detail.